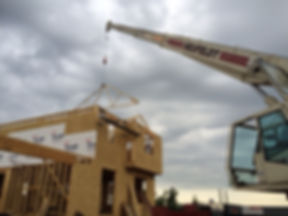
The Hoist-Riteâ„¢ Model 1622 spreader beam is the ideal solution for safely lifting large or expansive objects. Each end of the spreader beam adjusts outward from the center in one-foot increments, spanning from 16 feet to 22 feet. By making both ends adjustable, the 1622 remains more balanced than spreaders that use a single point of adjustment. This is because on the 1622 the heaviest section remains centered over the load, providing strength and support where it is needed most.
Designs that employ a single point of adjustment have one end that is heavier than the other, which can create an out-of-balance situation and can put undue stress on rigging components. When matched with Neufab’s Gripper™ Truss hooks, the 1622 becomes part of the perfect truss handling solution that is capable of quickly and safely handling even the largest of wood trusses.
The Hoist-Riteâ„¢ Multi-Lift Model 72 spreader beam is designed for use when handling multiple trusses such as in a high volume, production-building environment. Rather than hoisting trusses into place singly, which can be a slow and tedious task, up to five, pre-spaced trusses can be hoisted at one time. Alternatively, framing crews can build roof subsections from the safety of the ground before flying the entire assembly swiftly into place in one easy motion. As the first subsection is being anchored in place, crewmembers on the ground can be assembling a second subsection. The resulting savings in man-hours can be significant.
The Multi-Lift spreader features mounting holes for industry-standard shackles and rigging spaced at both 16-inch and 24-inch intervals. Combine the Multi-Lift with a set of Model 1622 spreader beams and Gripperâ„¢ Hooks for the ultimate truss handling system that provides unmatched speed and safety. Such versatility increases the return on investment because it allows the Multi-Lift to be used on the complex roof designs of today and tomorrow.
The Slip-N-Pinâ„¢ Model 60 is a unique, adjustable spreader beam design that showcases the innovation and versatility found in all Neufab products. The spread of the Slip-N-Pinâ„¢ can be adjusted easily by removing the quick-release pins, aligning the movable end-caps with any one of the pre-set holes, and re-inserting the pin. In addition, the Slip-N-Pinâ„¢ is available in a variety of lengths to suit your application.
In its basic configuration, the Slip-N-Pinâ„¢ is great for general lifting purposes, or it can be paired with optional Gripperâ„¢ Truss Hooks, as shown above, to form a complete roof truss handling solution. The eyelets on the sliding end-caps have been engineered to accept industry standard shackles or Gripperâ„¢ Truss Hooks, and reconfiguration takes just seconds. The Gripperâ„¢ and Slip-N-Pinâ„¢ combination is ideal for safely handling small to mid-sized wood trusses.
Safety is no accident. Fall Protection is OSHA’s third most commonly cited safety violation. According to the National Safety Council, there were 5,680 such violations in 2004. With site inspections on the rise, why take the risk? Both OSHA safety inspectors and insurance companies have raved about improved worker safety when using the Gripper™.
Proper use of the Gripperâ„¢ prevents falls because workers no longer have to climb onto unstable trusses to disconnect rigging harnesses. Instead, a worker standing on the ground releases the hook by way of a release cord. It is the only system of its kind on the market and meets OSHA regulations for a closed-loop lifting system (OSHA 1926.550). In addition, each Gripperâ„¢ Hook goes through a rigorous quality inspection process and is stress tested before it leaves the factory to ensure that it will provide years of trouble-free service.
Cost Counts. At a time when construction costs are rising almost as fast as healthcare costs, it pays to find new ways to reduce overhead costs. Because the Gripperâ„¢ reduces the time required to lift and set trusses, valuable savings can be achieved on labor and crane rental charges. A reduction in the likelihood of fall-related injuries provides additional cost savings.
Depending on the size of the project, cost savings can equate to several thousand dollars, meaning that the Gripperâ„¢ can easily pay for itself after only one job. Consider that the cost to rent a crane with an operator is approximately $150 per hour; add to that the cost of labor at $25 per hour per man. In addition, the average medical cost to treat a broken arm, a common and relatively minor fall related injury, is $1100. Every injury prevented and every hour saved reduces overhead costs and increases profitability of the project.
Time is money. The Gripper™ Truss Hook offers a revolutionary way to handle wood roofing trusses quickly and easily. Its patent pending design reduces labor costs, improves worker safety and helps to ensure regulatory compliance. The Gripper™ speeds up the construction process because more trusses can be set in less time. Timesaving’s over conventional methods of 50% or more, on average, are possible, which allows for more aggressive bidding
Traditionally, roofing trusses are hoisted into place by cranes using slings or rigging that, according to Occupational Safety & Health Administration (OSHA) regulations, must be securely attached to the truss. Attaching and detaching the rigging takes precious time. Once the Gripperâ„¢ has been positioned on the truss, a worker pulls the trigger mechanism, causing a spring-actuated cam with serrated teeth to bite into the truss, securely holding the hook in position. After the truss is set, the worker pulls the unlocking cable, releasing the Gripperâ„¢ from the truss. While the framing crew anchors the truss, the crane operator can move to the next one.